Nar Alzayt; 1939
- Mike
- Jun 2, 2024
- 6 min read
Updated: Jun 3, 2024

Elephant Rock (Jabal AlFil ) At Alula; جبل الفيل
Part 3; Dammam No. 12; حريق
After the success of the No. 7 well at Dammam, CASOC stepped way out on the structure and found the oil-water contact in the Arab C zone; the well flowed 5,000 BWPD like an artesian well. It was temporarily shut in and the 9, 10 and 11 wells all made good oil producers up-structure.
Two more skid-mounted drilling rigs were shipped from Bahrain, more men arrived from the States to manage them, both Halliburtion and Schlumberger sent cementing and open-hole logging trucks to Saudi Arabia in late 1938 and stationed them in the camp at Dhahran on 24 hour standby. With men came wives, and children, and more central air units.
While part of Max Steinike's geological staff managed the development of the Dammam Dome, the other half of the division scoured the desert looking for more prospects to drill. Aerial photography were tied to magnetics and gravity studies and Schlumberger resistivity logs run in new, open hole wells gave insight into permeability and porosity. Slowly but surely the big picture came together and better wells were being found. The 8 inch OD pipeline from Dammam to Al-Khobar on the coast was finished and a daily circulation of barges crossed the Arabian Gulf carrying Dammam oil to the BAPCO refinery in Bahrain.

So it was in June of 1939 when 6 inch production casing was run to the anhydride bed below the Arab C zone at 4,700 feet TD and cemented to surface in the Dammam No. 12. The upper section of the "C' zone was perforated (holes shot thru the casing and surrounding cement sheath) to provide small diameter flow paths from the formation to the well bore. Initial testing of the upper section was encouraging and the well was tested for ten days flowing 1,400 BOPD of oil and gas to the surface.
On the left, a perforating gun with pre 1965 steel bullets all interconnected with primer chord and an explosive charge that was set-off with a "g0-devil," an iron ring that slid down the wire line striking the denotating cap and setting off all the perforation charges simultaneously.
By open-hole electric logs and lithology samplying of the drill cuttings there appeared to be an additional 100 foot section of very porous rock in the C zone and mangement decided to add those perforations in hope of increasing production. July 4th was celebrated by Americans back in camp and by the 6th of July equipment was prepared to re-perforate the No. 12 well.
Master valves were shut in on the production tree and a 30 foot, 4 inch OD lubricator device was rigged up on the 6 inch production casing above the valves that would allow the new perforation gun to be lowered to the new zone of interest with the well under pressure. A rubber pack-off element squeezed tight around the wire line allowed all this to happen without making a mess and maintaining pressure control at the surface. This was all standard operating proceedure for hands involved and no one was particularly concerned about the well prodeedure.
On a balmy 125 degree afternoon on July 8th, men were in the cellar checking valves and making last minutue preparartions. The perforating gun was lowered into the lubricator, the wire line squeezed tight and the master valve on the production tree opened to lower the gun to the desired depth.
Likely because of shut-in pressure buildup when the master valve was opened, the peforating gun was blown into the top of the lubricator inadvertanly setting off the blasting cap and detonating the peforating gun. The well exploded and broke windows back at camp. Fire blew straight up the 6 inch casing 200 feet into the air. One Saudi was killed immediately and one American died the next day of severe burns. Within two hours the standard derrick melted and collapsed.

Unrestricted, the well was estimated to be spilling 8,000 BOPD onto the desert. That portion of it not being burned off was gathered in enourmous earthen pits.
Most of the American drilling personal in Eastern Saudi Arabia in the late 1930's had been around the world drilling wells in places like Borneo, Venezuela, and Canada and blowouts were fairly common place. They had a sense of what to do.
The 8 inch OD oil pipeline to the coast was flushed out and reversed, providing sea water for cooling and being able to work around the fire. The No. 8 well was opened providing unlimited sea water for the steam boilers, mud pumps and a brand new fire truck for the camp sent from California a few weeks earlier. Requests for certain equipment and supplies to fight the fire were slow in coming as most of it had to come from Europe where WW II was about to get underway. Myron Kinley, living in Los Angeles in 1938, was telegraphed. He was in Louisiana on a big fire but believed he could fly to Bahrain within 4 days. He was put on standby.
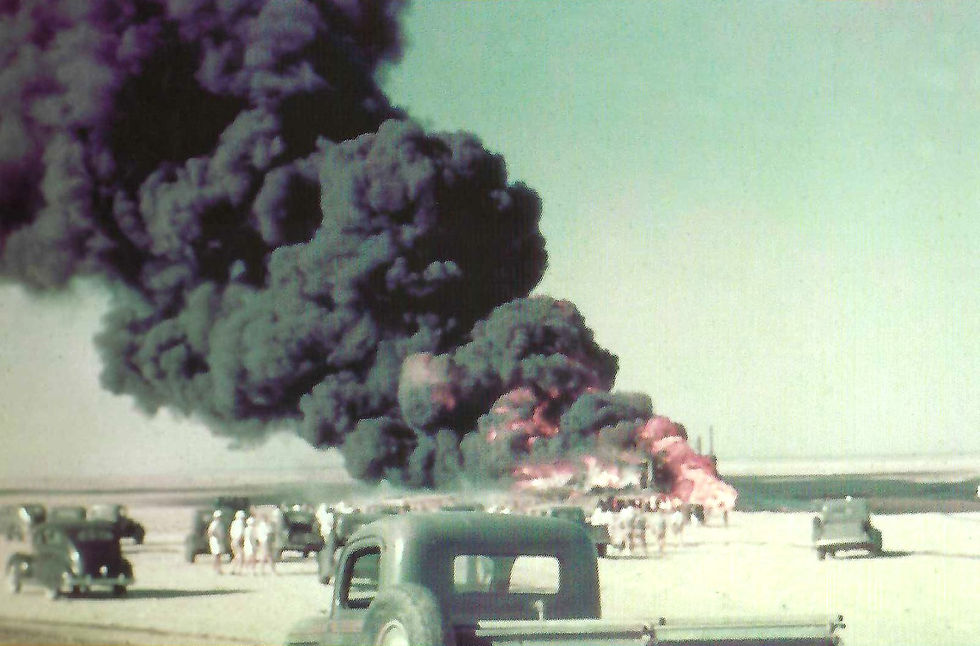
Geologists, engineers, roughnecks, cooks and camp cleaning people were all assigned to the Damman No. 12 disaster. Meetings were undertaken and it was decided under the direction of Floyd Ohliger, the chief drilling engineer, that CASOC would attempt to control the blowout themselves. There was concern for loss of bottom hole reservoir pressure and that the remaining valves on the production tree being destroyed under intense heat. Time was of the essence.
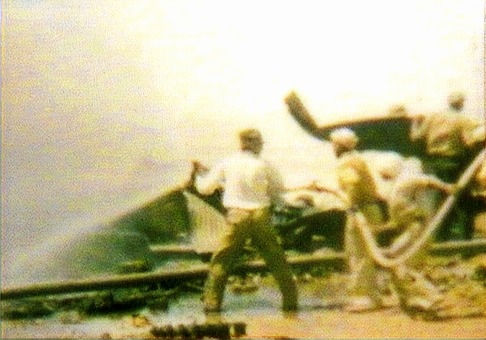
When the perforating gun prematurely went off it disinegrated the lubircator and blew two of the three valves off the production tree above the master valve. All the uncontrolled flow was coming straight up 6 inch casing thru a 4 inch OD swedge.
Heat shields were built and an airplane from London arrived with air packs, asbestos suits, spray nozzels, and more pumps for water.
Enough pressurized steam from the boilers and the new, shiney fire truck, allowed two Oklahomans to get close into to the well head and partially close the master valve below the 6 to 4 inch swedge. This reduced flow rates signficiantly. Before being able to close the valve entirely the stem to the gate broke off. One of the Oklahomans collapsed and had to be drug off the rig floor, out of harms way.
A sort of large, umbrella-like cap, called a spoon, was built in the machine shop in Dhahran and drug over the flow with side-boom pipeline dozers and anchored down; the handle to the spoon-like cap was 4 inch OD pipe. Once in place large volumes of oil flowed down the outlet and into hoses that carried oil to earthen puts. This caused the fire to go down and bellow under the rig floor. Flow rates diminished signficantly. But as the fire was reduced concerns about H2S gas grew.
The entire camp at Dhahran was abandoned and all the women and children sent to Bahrain. Massive amounts of sea water were turned under the rig floor and into the cellar further dimenishing the fire, and ensuing heat. This water flow helped carry oil to earthen pits and reduced the fuel source to the fire.

With flow rates diminshed and the fire not as intense, men were able to devise a means of tapping a large diameter hole into the 4 inch OD flow line immediately below the Master valve. Basically this involved drilling into the flow line with a large bit while the flow line still under pressure, a practice still used in well control today called, "hot-tapping." Once the tap was complete the bit could be removed and the new inlet/outlet let below the partially closed master valve was nippled up to pump trucks. Heavy drill mud was built to 12 pounds per gallon density and stored in nearby pits.
At Dammam No. 12, the hot tap was made on June 18th, 10 days after the well blewout. Mud was immediately bull-headed (pumped against pressure) down the 6 in. casing and within two hours the fire was out and well rendered completely dead. Hundreds of barrels of additional heavy mud were pumped, just in case.
The evening of the 18th, with the No. 12 well silent after ten days, and the entire camp relaxed in exhaused jubilation, Floyd Ohliger wired headquarters in San Francisco. It read:
FIRE EXTINGUISHED, STOP. HOLE FULL OF MUD, STOP. PROFESSIONAL FIRE FIGHTERS NOT NEEDED, STOP.
Please click the image above to access another short film of Dammam 12.

2024, The Port of Dammam, Dhahran, Saudi Arabia
Dammam Dome produced approximately 200 MM BO from 21 wells; exact producton statistics are rarely known in the KSA. The field was shut in completely beginning in the late 1970's for economic reasons. The field is known to contain 500 MM BO of remaining recoverable oil from known, proven formations in the upper Jurrasic Arab, but is being shot extensively with 3-D sesimic data looking for new, deeper secrets. ARAMCO anticipates new developments in the field by mid year 2025 will result in 100,000 BOPD.
Next, In Part 4;
The Great Arab D Zone
Nar Alzayt is Arabic for oil fire.
Author's note: this is all for fun, to simply summarize an important milestone in the history of world oil and gas. There are countless articles and papers about the first discovery in Saudi Arabia, all far better and more historically accurate than mine. I hope what I have done is stir your interest.
I am sorry for any misuse of the Arabic language or any mistakes I might have made with regard to facts. Again, I am hitting in the high points. This is a four part serices and I will acknowledge all of my sources and references at the end of Part 4.
Comments